Pre –Receiving Operations
Preparation for Goods Receiving
- In the process of preparing for the receipt of goods, warehouse managers should develop and enforce receiving requirements for suppliers, shippers, and/or carriers in order for the warehouse receiving process to work well.
- The goal is for them to offer the goods in such a way that it can be processed quickly and easily.
Receiving Requirements
- Packaging requirements should be communicated early to suppliers and where possible standardized: these include; Label position, Label information, Palletized or loose cargo, Number of packages per pallet, Items per carton, Acceptable package size and weight
- Shippers or customers who don’t have control over packing or packaging requirements should be required to offer clear, detailed information and alert the warehouse of new incoming shipments.
- Transporters should load cargo according to the order of the delivery route and should have all documentation in hand when they arrive to the receiving area.
- In order to speed up the receiving process and reduce cargo damage, suppliers should be required to palletize cargo before it is sent to a warehouse.
Labour Requirements
- Labour is ranked among the highest warehouse operational costs, it therefore very important to match the work load and the work force.
- The volume and type of cargo to be received should be matched with available human resources and equipment in order to avoid labour shortages or idle labour in the warehouse.
- The warehouse management should determine the time and dates when cargo is delivered and received.
- Warehouse managers can use a booking or scheduling software where the carrier can pre-book the delivery and the warehouse manager can review and process the bookings.
Unloading Requirements
- The main goal during the unloading process is to unload cargo safely and efficiently. This includes checking seals, capturing temperature details for perishable goods, and verifying the booking references.
- The appropriate equipment should be availed and labour hours should be properly allocated to ensure that the offloading process is done in a seamless way.
- When offloading palletized cargo, it is advisable to use power pallet trucks in order to optimize safety check and speed whereas for loose cargo it is recommended to use conveyors to minimise the safety and health issues related to using human hands.
Pre-receiving Documentation
Re-order notification
- The re-order notification is usually issued by the stock controller, and a copy is sent to the purchasing department and the receiving department. The purchasing department will place an order with the supplier and the receiving department will know that a delivery of goods is on the way to be warehoused.
Purchase order (PO)
- The purchasing department is responsible for issuing orders and seeing that a copy of the PO comes to the warehouse floor. The purchase order is usually a copy of the order placed by the warehouse, to replenish goods. This copy is kept on file in the warehouse and is used when deliveries arrive to be checked off.
Delivery note
- The delivery note usually comes with the goods when they are delivered. It tells the warehouse what the supplier has actually delivered to the store.
Consignment Note
- The consignment note is issued by the courier for the delivery of goods. The consignment note is written out when the delivery is contracted out to a third party for delivery, for example rail, post or a courier company.
Internal packing note
- An internal packing note is used when you carry out a more detailed check of the stock delivered. You make this check after you remove the goods from their outer containers such as cartons, drums or boxes, or you unload them from pallets. The internal packing note lists what is actually within each unit delivered.
Invoice
- An invoice is a commercial document indicating the products, quantities, and agreed prices for products or services the supplier has provided. An invoice indicates the sale transaction only. Payment terms are independent of the invoice and are negotiated by the buyer and the seller. Payment terms are usually included on the invoice.
Pre-receiving Packaging Requirements
“Packaging
Packaging is the act of enclosing or protecting products for distribution, storage, sale, and use.
- Package labelling or labelling is any written, electronic, or graphic communications on the packaging. Packaging can be described as a co-ordinated system of preparing goods for transport, warehousing, logistics, sale, and end use. Packaging contains, protects, preserves, transports, informs, and sells.
“Purpose of Packaging
Packaging and package labelling have several objectives including:
- Physical protection – The objects enclosed in the package may require protection from, among other things, shock, vibration, compression, temperature, etc.
- Barrier protection – A barrier from oxygen, water vapour, dust, etc., is often required.
- Containment or agglomeration – Small objects are typically grouped together in one package for reasons of efficiency.
- Information transmission – Packages and labels communicate how to use, transport, recycle, or dispose of the package or product.
- Marketing – The packaging and labels can be used by marketers to encourage potential buyers to purchase the product.
- Security – Packaging can play an important role in reducing the security risks of shipment. Packages can be made with improved tamper resistance to deter tampering and also can have tamper-evident features to help indicate tampering.
- Convenience – Packages can have features which add convenience in distribution, handling, stacking, display, sale, opening, reclosing, use, and reuse.
Labelling Requirements And Label Positioning
Symbols used on packages and labels
Many types of symbols for package labelling are nationally and internationally standardised.
- For consumer packaging, symbols exist for product certifications, trademarks, proof of purchase, etc.
- Some requirements and symbols exist to communicate aspects of consumer use and safety.
- Recycling directions, Resin identification code, and package environmental claims have special codes and symbols.
- Bar codes, Universal Product Codes, and RFID labels are common to allow automated information management.
- Labelling
Labelling of packaging for products or materials is critical for the storage and transportation of the goods. The label identifies the contents of the box/container and would usually include a barcode used for scanning and tracking the movement of goods
Common Markings and labels and those included in the ISO standard 780
- Packages are often marked with handling instructions in the language of the country of origin. While this may safeguard the consignment to some extent, it is of little value for goods consigned to, or through, countries using different languages, and of no value at all if people handling the packages are illiterate.
- Pictorial symbols offer the best possibility of conveying the consignor’s intention and their adoption will, therefore, undoubtedly reduce loss and damage through incorrect handling. The use of pictorial symbols does not provide any guarantee of satisfactory handling; proper protective packaging is therefore of primary importance.
Display of symbols
- Symbols should preferably be stencilled directly on the package or may appear on a label. It is recommended that the symbols be painted, printed or otherwise reproduced as specified in this ISO standard. They need not be framed by border lines. The graphical design of each symbol should have only one meaning; symbols are purposely designed so that they can also be stencilled without changing the graphics.
Colour of symbols
- The colour used for symbols should be black. Care should be taken to avoid the use of colours which could result in confusion with the labelling of dangerous goods. The use of red, orange or yellow should be avoided unless regional or national regulations require such use.
Size of symbols
- For normal purposes the overall height of the symbols should be 100 mm, 150 mm or 200 mm. The size or shape of the package may, however, necessitate use of larger or smaller sizes for the symbols.
Positioning of symbols
- Particular attention should be paid to the correct application of the symbols, as faulty application may lead to misinterpretation. Symbols No. 7 and No. 16 should be applied in their correct respective positions and in appropriate respective places in order to convey the meaning clearly and fully.
Handling instructions
- Handling instructions should be indicated on transport packages by using the corresponding symbols given in the following table.
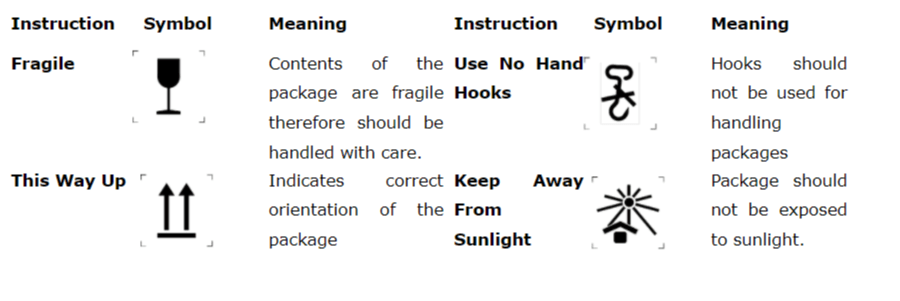
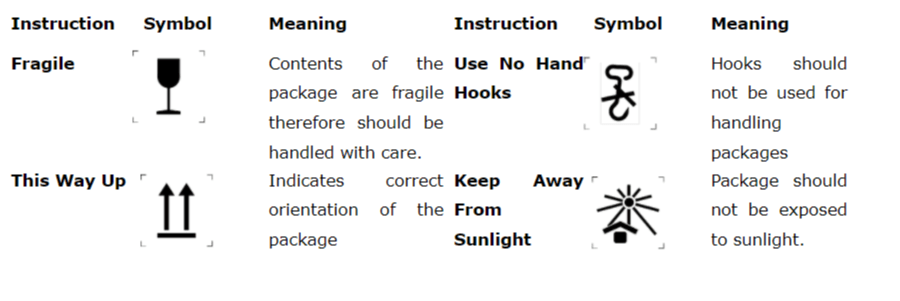
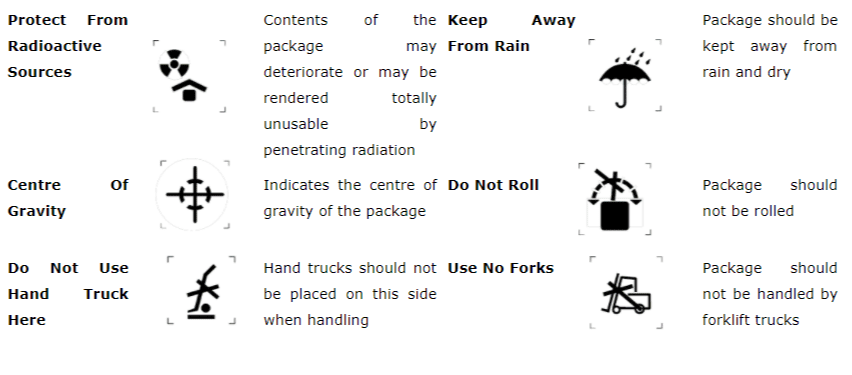
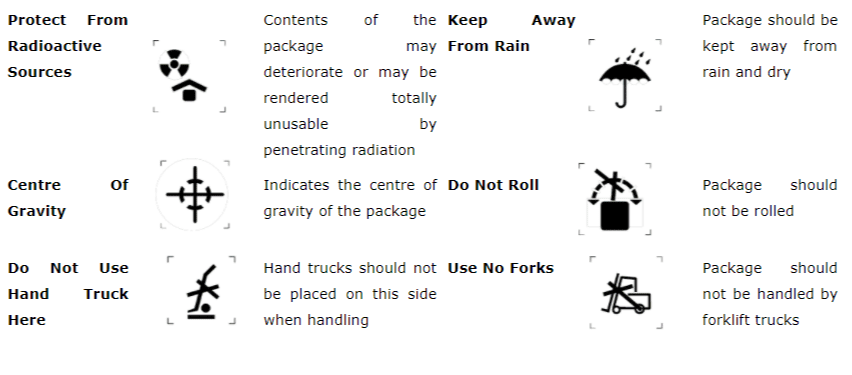
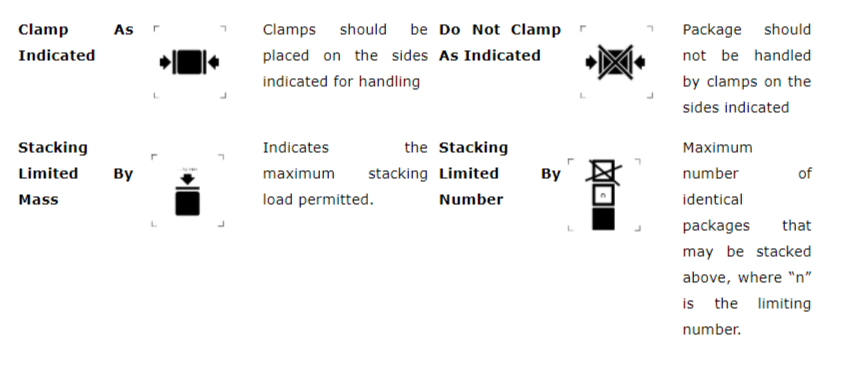
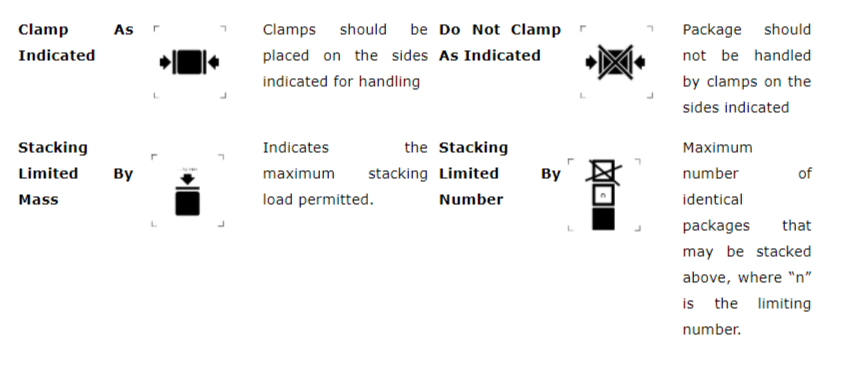
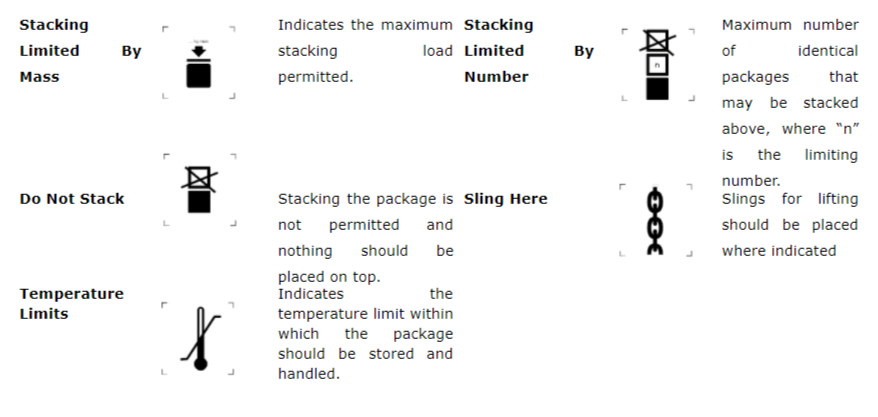
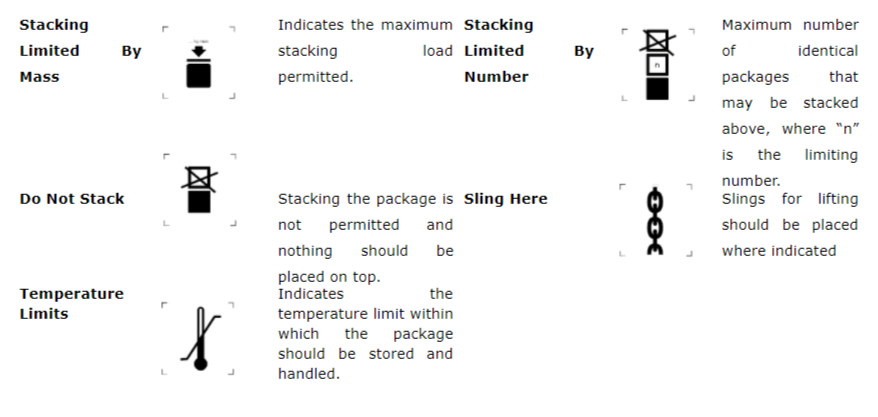
Information About the Goods to be Received
- Whether the cargo is loose or Palletized
- The dimensions of the outer package, (height, width and length) the weight of the packaged goods
- Protective requirements, for example, against temperature, dust or moisture
- Special handling, for example, certain chemicals should not be packed together
- Outer packaging requirements, for example, if thin outer cartons are used this will limit stacking due to the danger of crushing goods within the cartons
- The shape of the stock, not all goods pack neatly into a cube dimension, for example, lengths steel may be banded and moved using a specially designed cradle
- The labelling required, for example, information about dimensions and weight, or handling instructions such as symbols or written guides that must appear on the outer pack.
Self-Assessment Questions and Activities on Pre-Receiving Operations
- The pre-receiving process in a warehouse is as important as the receiving process itself. Discuss the above statement, highlighting the steps taken while preparing to receive goods in a warehouse.
- What major requirements have to be in place before goods are received in a warehouse?
- Describe six (6) key documents which are required at a warehouse during the process of receiving goods.
- Why do you think it is important that goods are packaged and labelled appropriately before being shipped to a warehouse?
- A consignment of COVID-19 Vaccines is about to be shipped to your warehouse, what kind of information would your require from the shippers about vaccines to be received.