Storage Equipment
Manual Storage Equipment
- Block Stacking
Block stacking is a form of palletised storage that does not require any type of storage equipment, and instead loaded pallets are placed directly on the floor and built up in stacks to a maximum stable storage height. Lanes are created to ensure access to the different stock keeping units (SKUs).
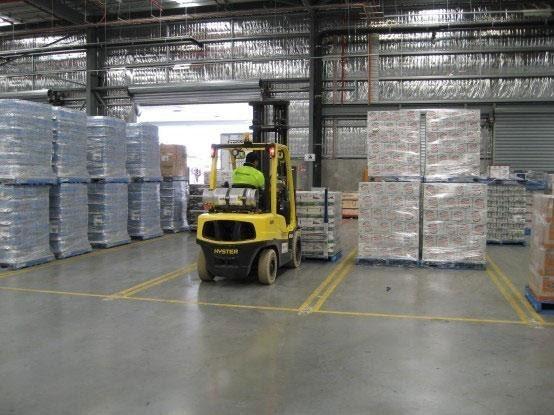
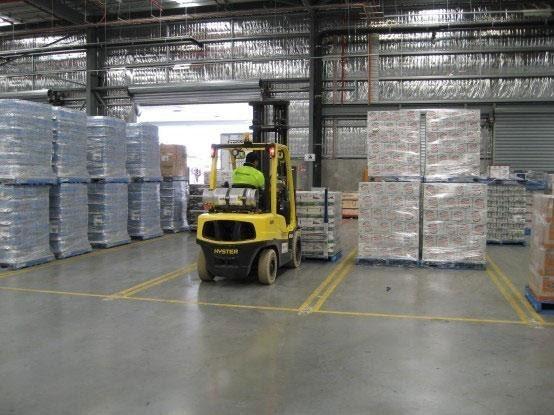
The maximum storage heights or stacking levels are determined by a number of different factors such as:
- Load strength (crushability)
- Load weight
- Load stability
- Pallet conditions
- Safety limits
- Weather (humidity, water, wind can weaken pallets and soften loads)
- Warehousing clearance heights
Advantages of floor stacking:
- Very low setup costs
- Flexible
Disadvantages of floor stacking:
- Low density storage (Requires a large storage facility to store only a small amount of stock).
- Poor ventilation of products
- Storage height depends on a number of variable factors
- Only one SKU can be effectively stored in a lane, empty pallet spaces are created that cannot be utilized effectively until an entire lane is emptied.
- You have to move the top pallet to get to the pallet underneath (LIFO).
Bin Shelving
- Bin shelving is designed to handle non-palletized loads and is generally used for small parts. Because items are hand-picked, bin height usually does not exceed seven feet, which may lead to cube space underutilization.
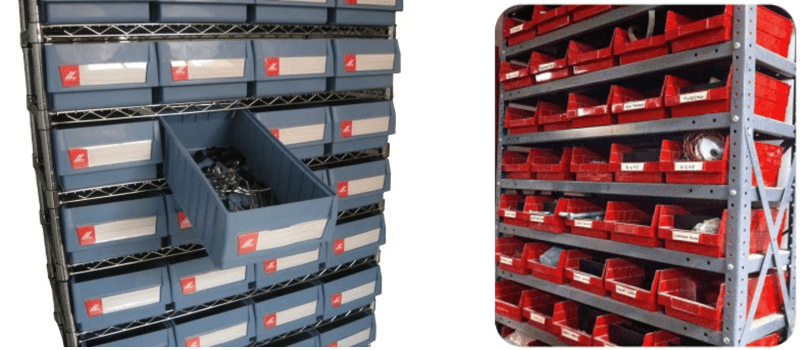
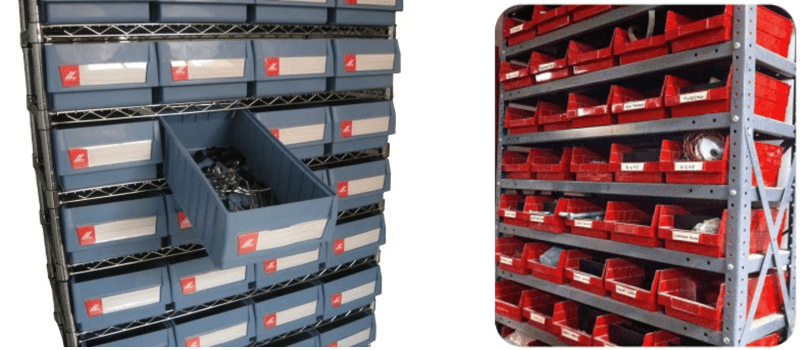
Modular Storage Drawers
- Modular storage drawers protect parts from the outside environment and allow for a higher concentration of stored items and increased picking accuracy. They also lead to underutilization of cube space. The drawers and their cabinets come in many sizes and combinations to accommodate one SKU or many SKUs. Specific SKUs are stored in each compartment, so picking accuracy should increase; however, because pickers have to reach into the drawers, the structure is usually limited to a height of about five feet, which can lead to an underutilization of cube space.
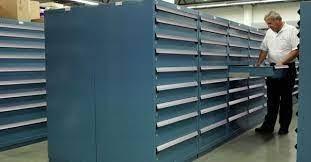
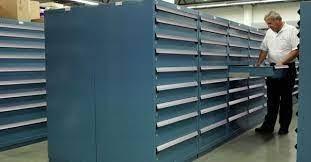
Static Shelving
- As the name suggests, static shelves are storage mechanisms that are designed to stay in one place. For the most part, they are meant to hold inventory that is fairly lightweight (a few hundred pounds per shelf). It’s commonly used for storing inventory that needs continuous replenishment. Because they’re not compatible with forklifts, static shelving is generally used with inventory that must be manually picked, placed, and/or organized.
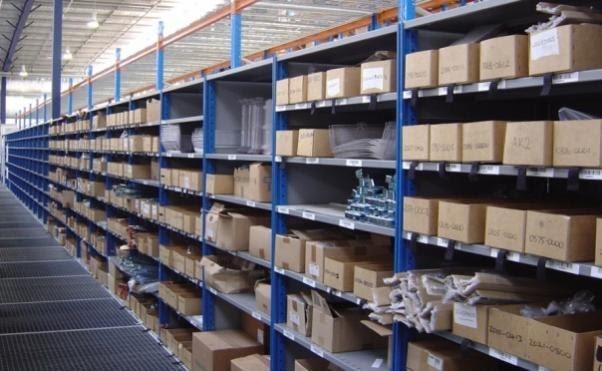
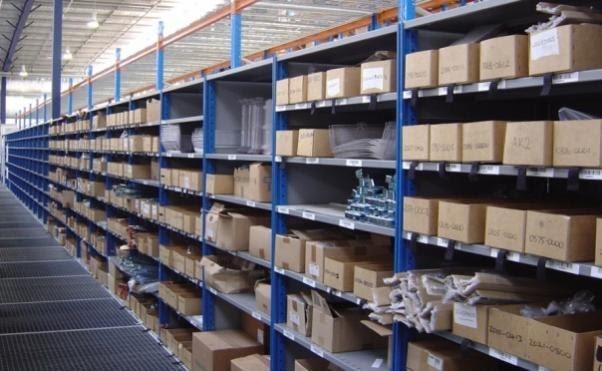
Mobile Shelves
- It is similar to static shelving, but the only difference is that it can move and offers adjustable shelves. Such systems are designed to accommodate more goods in less space. Some of them can also contain locking systems and level tracks. The level tracks can either be mechanized or manual.
Wire Partitions
- Wire partitions are secure wire cages, and sections are an essential accessory for improving warehouse security. They are typically made of fence-like wire mesh materials, creating a durable and robust enclosure that makes it easy to designate high-security storage areas or sections within your facility.
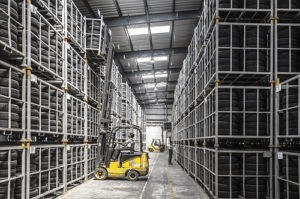
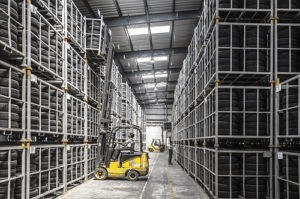
Mezzanine Flooring
- A warehouse mezzanine floor system is an elevated floor/platform that is installed between the floor and the ceiling. Most of the time these steel structures are free-standing and can be dismantled and moved with relative ease. Industrial mezzanines are normally composed of steel (carbon or stainless).
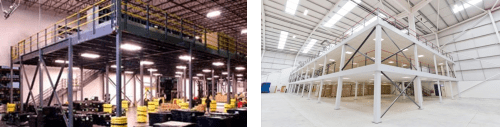
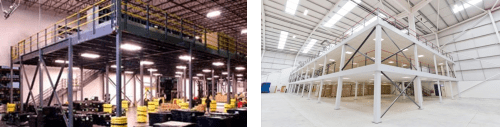
Racking
- Pallet Racking
- For the busiest and largest warehouses, pallet racking systems are usually treated as the centrepiece of the operation. Typically, pallet racking systems are made out of wood, metal, or plastic and hold inventory that is received in large boxes. Depending on the height, the boxes are placed on the pallet racking system with the help of a forklift or an automated mechanism.
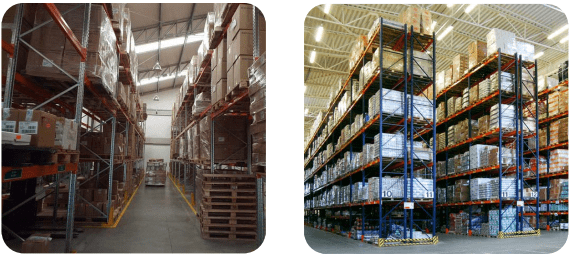
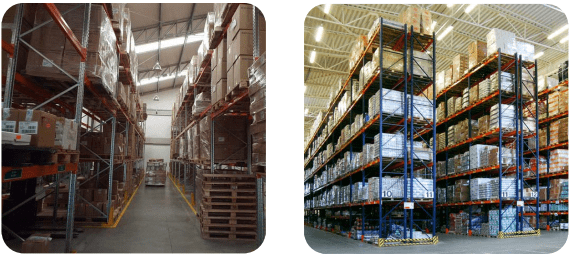
Multi-Tier Racking
- A great choice for large stocks of items that have small unit sizes, multi-tier racking is a system that is designed to capitalize on vertical space.
- Mostly, multi-tier racking concerns relatively lightweight items that are picked and organized manually.
Selective Pallet Rack
- Most popular type of storage rack
- Pallets are supported between load-supporting beams
- Special attachments and decking can be used to make the racks capable of supporting other types of unit loads besides pallets (e.g., coils, drums, skids)
- Selective racks can be used for the following types of storage:
- Standard—single-deep storage using a counterbalanced lift truck
- Narrow-Aisle—storage using a narrow-aisle lift truck
- Deep-Reach—greater than single-deep storage (typically double-deep storage)
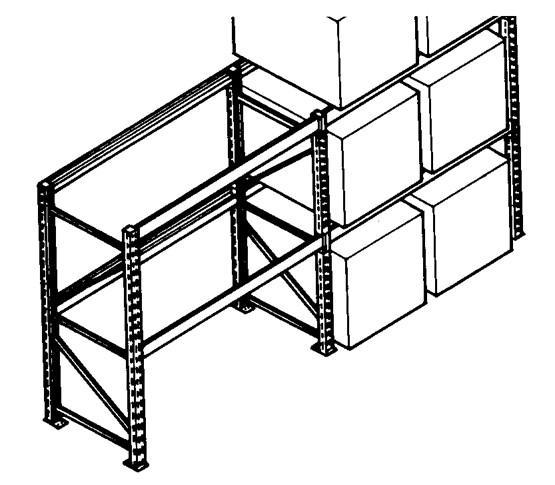
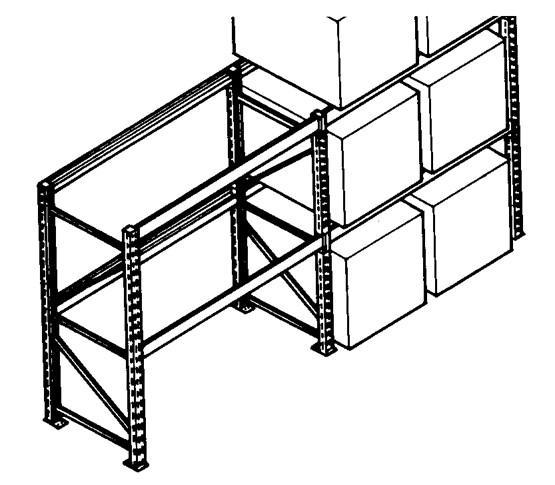
Drive-Through Rack
- Loads are supported by rails attached to the upright beams
- Lift trucks are driven between the uprights beams
- Open at both ends, allowing access from both ends (FIFO)
- Requires similar-width loads
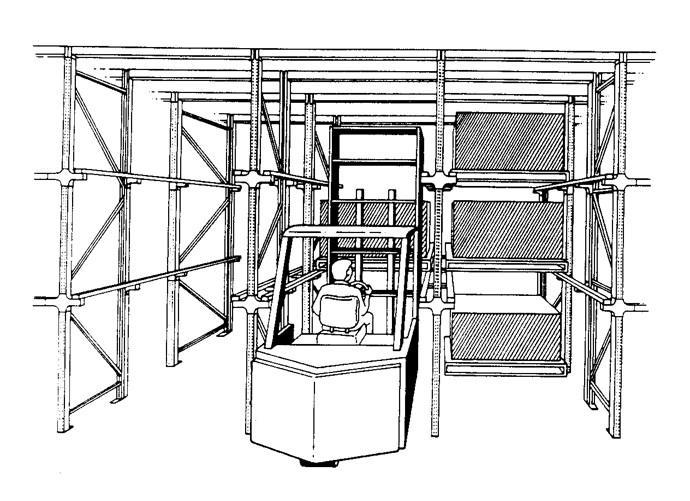
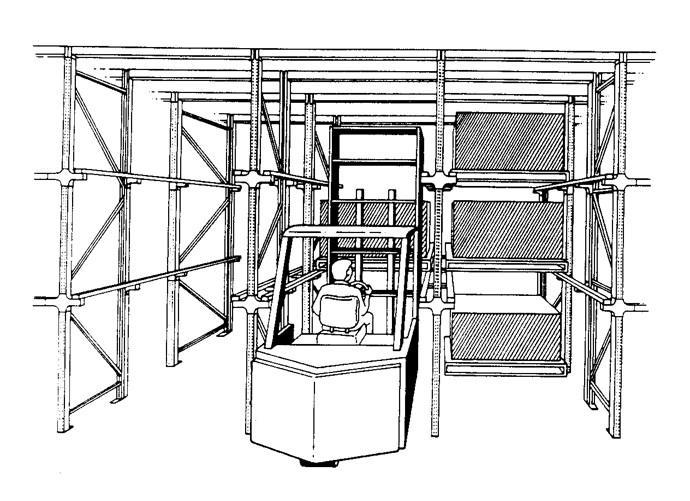
Cantilever Rack
- Loads are supported by cantilever “arms”
- Used to store long loads (e.g., bar stock, pipes, lumber)
- Similar to pallet racks, except the front upright beams and the front supporting beams are eliminated.
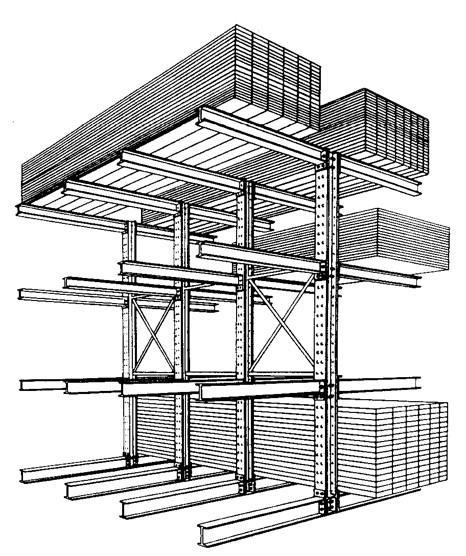
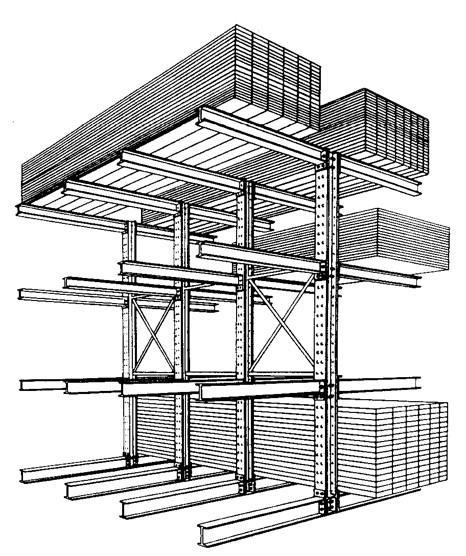
Automated Storage Devices
- Automated storage systems are designed for automated storage and retrieval of parts and items in manufacturing, distribution, retail, and wholesale.
- Advantages:
- fewer material handlers,
- better material control (including security),
- more efficient use of storage space
- Disadvantages:
- high capital and maintenance costs,
- difficult to modify
Unit Load AS/RS
- Used to store/retrieve loads that are palletized or unitized and weigh over 500 lbs.
- Stacking heights up to 130 ft. high, with most ranging from 60 to 85 ft. high; 5 to 6 ft. wide aisles; single- or double-deep storage racks
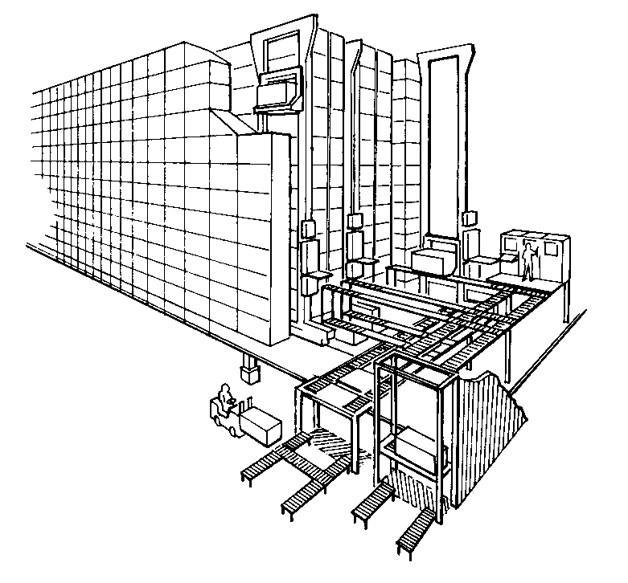
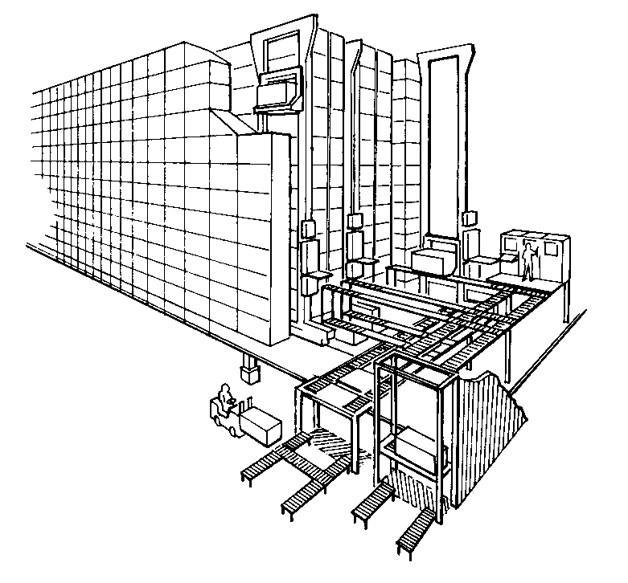
Miniload AS/RS
- Used to store/retrieve small parts and tools that can be stored in a storage bin or drawer
- End-of-aisle order picking and replenishment
- Stacking heights range from 12 to 20 ft.; bin capacities range from 200 to 750 lbs.
- Termed a “microload AS/RS” when used in assembly, kitting, and testing operations to deliver small containers of parts to individual workstations, where workstations are typically located on the sides of a pair of racks and the S/R machine operates between the racks to move containers to openings in the racks (storage lanes) located next to each station.
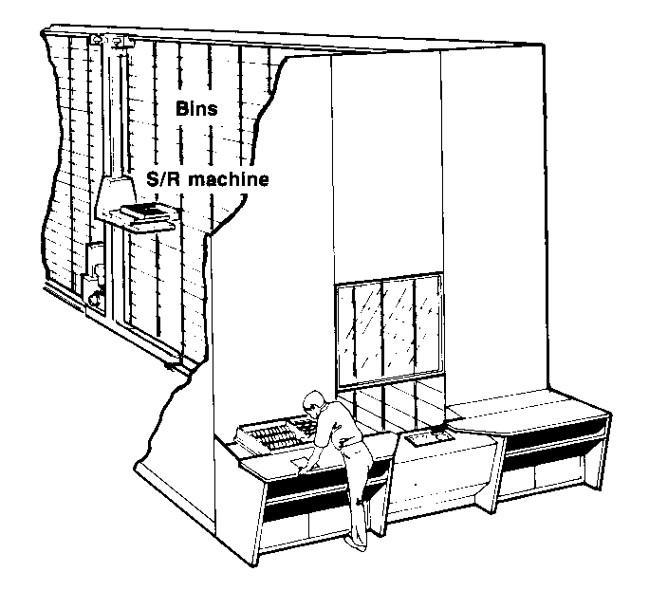
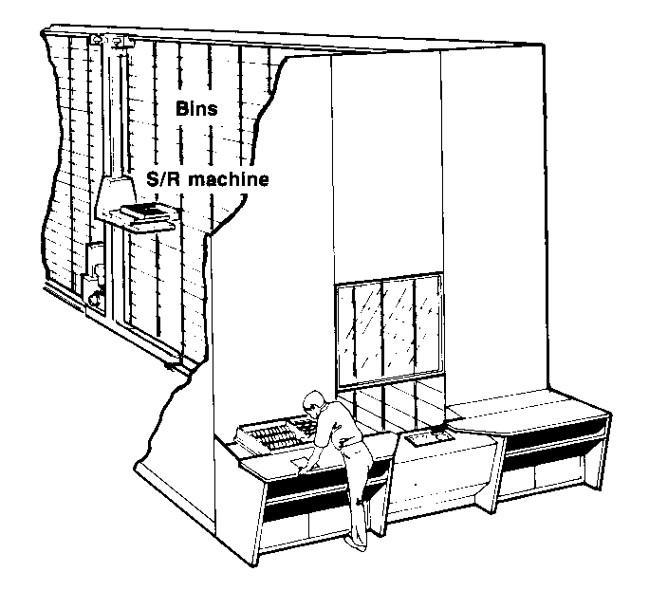
Man-On-Board AS/RS
- Used for in-aisle picking; operator picks from shelves, bins, or drawers within the storage structure
- Manual or automatic control
- S/R machine is similar to an order picker or turret truck and can sometimes operate as an industrial truck when outside an aisle, except the S/R is guided along a rail when operating in an aisle.
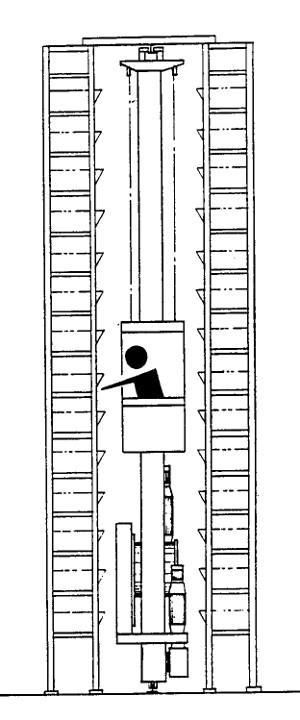
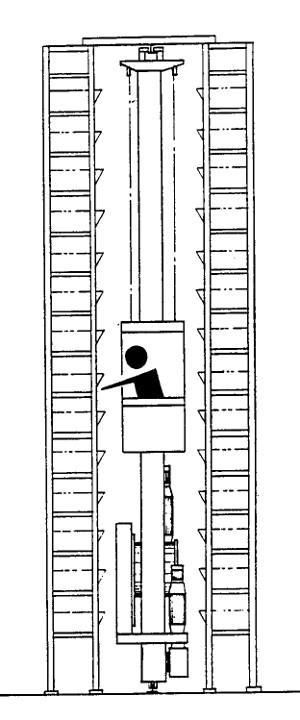
Deep-Lane AS/RS
- Similar to unit load AS/RS, except loads can be stored to greater depths in the storage rack
- A rack-entry vehicle is used to carry loads into the racks from the S/R machine, and is controlled by the S/R machine Termed an “automated item retrieval system” when used to automatically retrieve individual items or cases, with replenishment (storage) taking place manually from the rear of a flow-through storage lane and items are pushed forward with a rear-mounted pusher bar for automatic picking from the front of the storage lane.
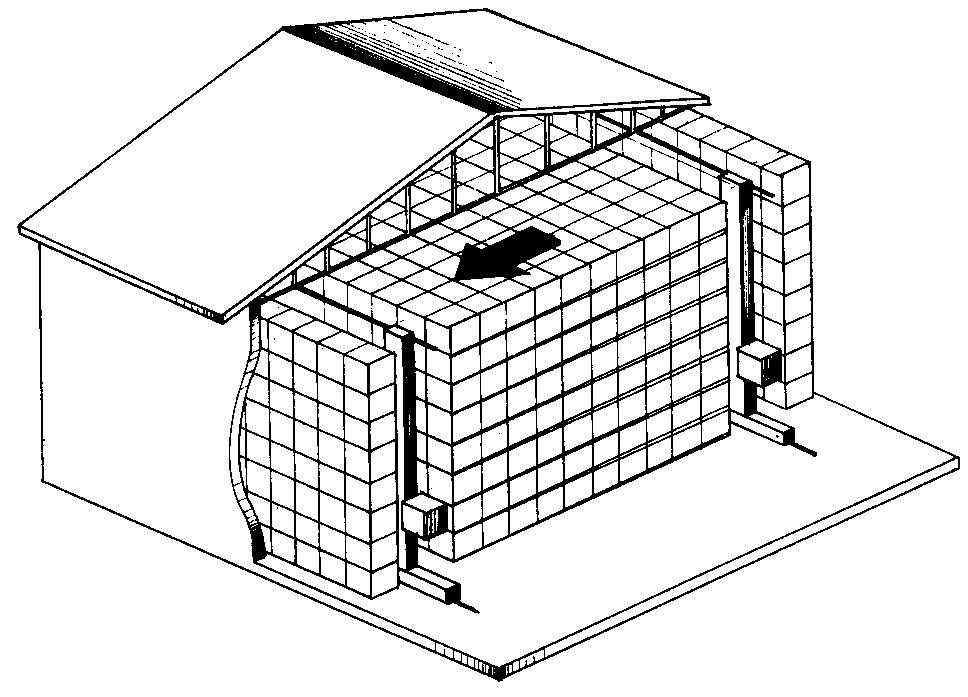
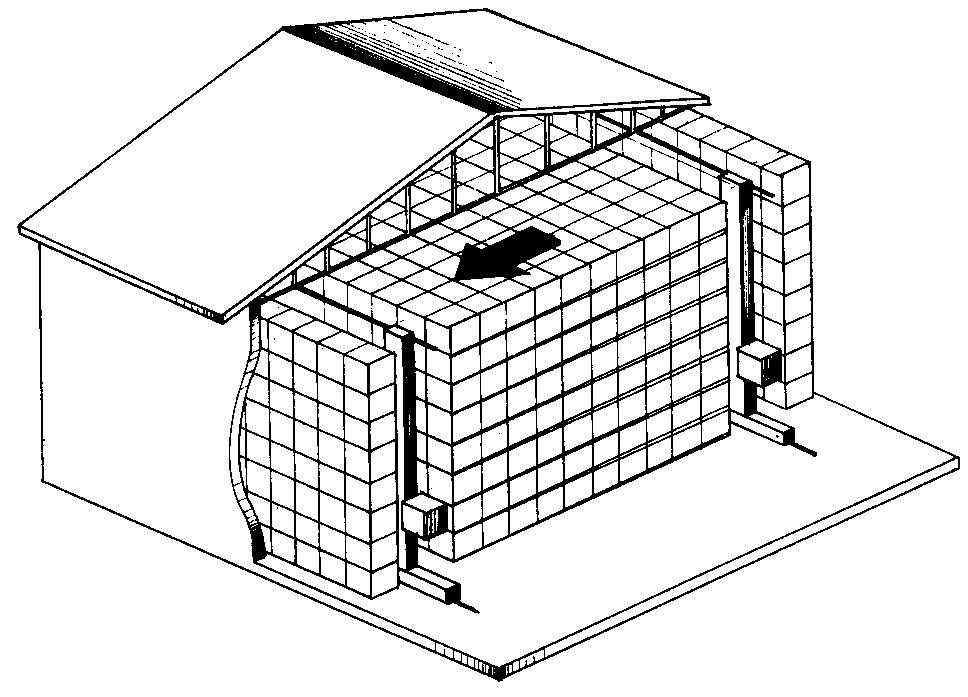
Carousels
- Carousel consists of a set of vertically or horizontally revolving storage baskets or bins. Materials (and the storage medium) move to the operator, “part-to-man,” for end-of-aisle picking.
- Each level of the carousel can rotate independently in a clockwise or counter-clockwise direction Control ranges from manually activated push buttons to automated computer controlled systems.
- Provides an alternative to typical “man-to-part” AS/RS, where the S/R machine moves to the part.
- There are the two major types of carousels:
- Horizontal carousel: consists of a series of revolving bins or shelves driven by a motor
- Vertical carousel: carousel that rotates bins or shelves along a vertical enclosed loop
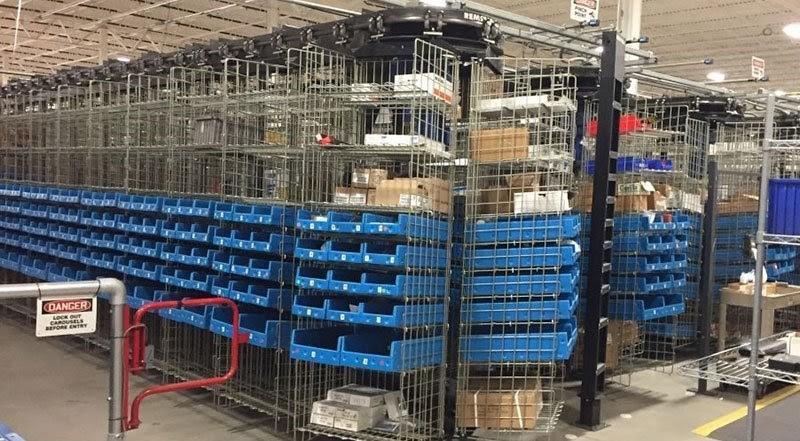
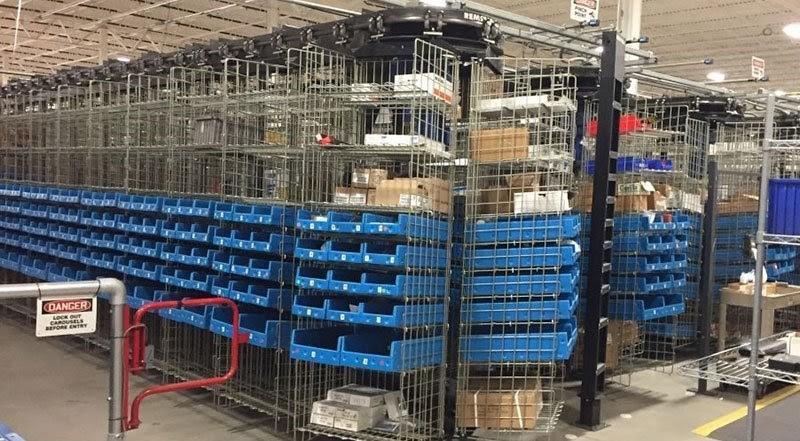